Health and health risks, know-how and emergencies
In the cosmetics and pharmaceuticals industry, managing health and quality risks is just part of doing business. Although there are constantly evolving standards in place to protect consumers, such as the WHO’s Good Manufacturing Practices (GMP), or the PIC/S (Pharmaceutical Inspection Co-operation Scheme) standards, post-marketing incidents occur regularly. This is…
In the cosmetics and pharmaceuticals industry, managing health and quality risks is just part of doing business. Although there are constantly evolving standards in place to protect consumers, such as the WHO’s Good Manufacturing Practices (GMP), or the PIC/S (Pharmaceutical Inspection Co-operation Scheme) standards, post-marketing incidents occur regularly. This is also true in the medical field. The French Nuclear Safety Authority (ASN) regularly reports accidents related to use of faulty equipment emitting ionising radiation for radiotherapy or brachytherapy treatments, for example. When responding to health emergencies, Stelliant Loss Adjusting puts its health experts to work for insurers and their professional clients to help them quickly recover from the crisis.
Types of health risks
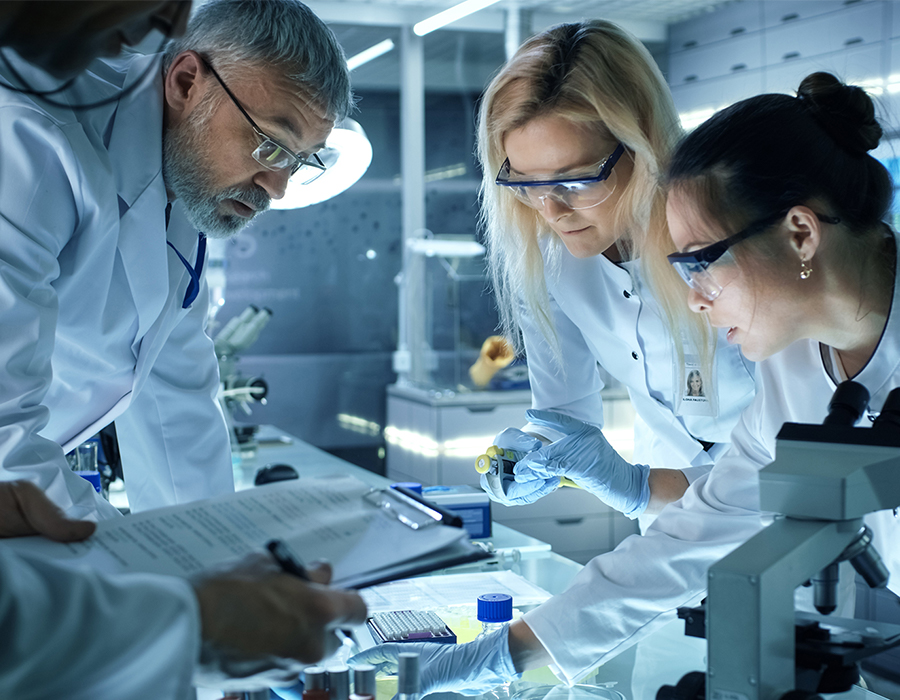
Cosmetic and pharmaceutical products are subject to strict regulation before being put on the market. Yet upstream controls don’t prevent incidents from occurring, and they are often reported by consumers themselves. These incidents can involve metal, organic or mineral foreign bodies contaminating a product (dust, fragments, fibres, particles, etc.), microbiological contamination (bacteria, parasites, viruses, etc.) or stability problems (deterioration in colour or fragrance, etc.).
In cases of proven or suspected health risks, the contaminated cosmetic products or non-compliant pharmaceutical products are systematically and immediately recalled.
Other types of incidents involving medical equipment can also pose health risks:
- CT scan or x-ray equipment failure,
- Contaminated site (operating rooms, sterilising rooms),
- Breakdown of a cold room for storing medication,
- Leak in a pipe carrying radioactive effluents used for metabolic radiotherapy,
- Overexposure of medical staff despite radiation protection, etc.
In these situations, the ultimate consequence is the complete shutdown of the compromised department or facility.
Whatever the type of incident, the response should be quick. Stelliant Loss Adjusting known what is at stake (in terms of health, finances, people and more) in these types of claims. That’s why our loss adjusters are ready with the responsiveness, professionalism and the teaching skills necessary to explain the reasoning behind the process to those they are working with.
A pragmatic, responsive and comprehensive solution
From pharmaceutical or cosmetic loss adjusting to complete crisis management, Stelliant Loss Adjusting understands all the procedures forwards and backwards. It provides insurers and their clients with comprehensive support, tailored to every problem.
Our loss adjusters are well aware of how urgent these situations are, and are able to offer concrete, financially viable solutions, based on initial background work on the timeline of events.
They then assess how much of a threat the incident poses to consumer health, studying the compromised cosmetic or pharmaceutical products, analysing the defective radiation equipment, doing a stocktake of products sold, etc.
Their mission is clear: find the source of the contamination and/or malfunction (during production, packaging, etc.) and identify the batches affected when the incident involves pharmaceutical or cosmetic products. All this to rapidly bring the incident under control by taking the contaminated batches off the market, under the terms of the product civil liability insurance, or by monitoring what is done with the radioactive equipment. Lastly, they support the policyholder through the recall process and offer solutions to continue production or reopen the health care facility once conditions are safe again.
There are several goals: quickly determine the causes of the incident and who is liable, protect people’s safety, and contain the impact on the company affected. Another goal is minimizing financial losses and reassuring consumers. Lastly, to help things get back to normal, Stelliant’s work also involves helping the manufacturing process resume and enabling facilities to reopen.
Loss adjusters at the centre of the quality process
To ensure that its pharmaceutical, cosmetic and health loss adjustments are as solid as possible, Stelliant Loss Adjusting selects experts from within its network with specific industry skills:
- Operational experience in pharmaceutical, cosmetic and health crisis management;
- Advanced technical skills in chemistry, microbiology, etc.
- Constant regulatory watch for any new standards in health risk management, such as the French Standardisation Association’s (AFNOR) ISO 16637 standard of June 2019, setting minimal requirements to be implemented in nuclear medicine to protect professionals.
With a perfect grasp of the methodology, they compile reliable, understandable and objective loss adjustment reports. Their technical and relational skills complement one another. Their role: help policyholders manage a crisis situation, while minimizing both material and intangible losses as much as possible. Depending on the situation, they may turn to other resources within the Stelliant Group: financial loss adjusters to assess financial losses on high stakes claims, industrial health risks loss adjusters for incidents involving equipment or processes, etc… A synergy of skills, all leveraged on each case to offer a comprehensive response with no grey areas.
key figures
years
of experience
cases
handled each year
loss adjusters
specialists